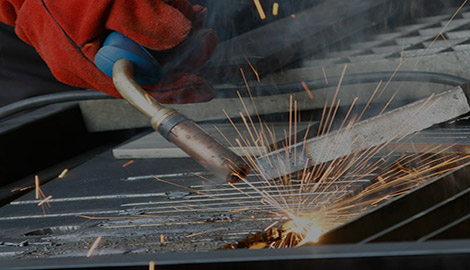
بهینه سازی فرایند جوشکاری نقطه ای
بهینه سازی فرایند جوشکاری نقطه ای
جوشکاری نقطهای را میتوان به روشهای متنوعی ارتقاء داد. ارتقای این فرآیند با انتخاب ماشین جوشکاریِ مناسب شروع میشود. از دیگر روشهای ارتقاء میتوان به رسیدن به تعادل حرارتی مناسب در فرآیند جوشکاری و استفاده از سیستمهای کنترلی پیشرفته اشاره کرد.
استفاده از جوشکاری مقاومتی نقطهای در صنایع مختلف مانند باتریسازی اتومبیلهای برقی
کایزن (Kaizen)، یا بهبود مستمر، یک اصل مهم و اساسی در فرآیند تولید محسوب میشود. این بدین معناست که کمتر از حد مطلوب هرگز قابل قبول نیست. تجلی این مفهوم را میتوان در فرآیند مونتاژ قطعات بهصورت عمده، که شامل عملیات جوشکاری مقاومتی نقطهای است، مشاهده کرد.
جوشکاری نقطهای شامل تولید گرما در سطح مشترک قطعاتی است که باید با عبور جریان الکتریکی در مدت زمان مشخص و فشار لازم به یکدیگر متصل شوند. مهندسان با تعیین دقیق بهترین ترکیب از پارامترهای زمان، نیرو و جریان الکتریکی، جوش محکم و مناسبی به دست میآورند.
از فناوری جوش نقطهای بهشکل گستردهای در صنایع خودروسازی، صنعت هوافضا، کارخانههای باتریسازی خودروهای برقی و البته لوازم خانگی استفاده میشود. این فناوری، سریع، مقرون به صرفه و به اندازۀ کافی منعطف در ایجاد جوشهای آلومینیوم به آلومینیوم و فولاد به فولاد است.
تام اسنو، رئیس هیئت مدیره شرکت T.J. Snow Co. توضیح میدهد: «با اینکه فناوری جوشکاری مقاومتی نقطهای، سریعترین راه برای اتصال ورق و تولید قویترین پیوندها در این نوع از فلزات به شمار میرود، با خود چالشهایی را نیز به همراه دارد.» همچنین ادامه داد: «برخلاف جوشکاری با قوس الکتریکی، اُپراتورهای این نوع از سیستمهای جوشکاری نمیتوانند بهسادگی به قطعه نگاه کنند و مطمئن باشند که اتصال جوش مناسب است. ممکن است خوب به نظر برسد، اما فقط با استفاده از میزان حرارت مناسب، نیرو و مدت زمان کافی و سپس آزمایش اتصال، این کاربر نهایی است که میتواند مطمئن شود که جوش از مقاومت لازم برخوردار است.»
شرکت T.J. Snow Co. از سال 1963 به ساخت و تعمیر سیستمهای جوشکاری مقاومتی نقطهای (از نوع سفارشی) اقدام کرده است. این شرکت را میتوان از جمله شرکتهای پیشگام در این حوزه دانست. سال گذشته، این شرکت یک دستگاه ماشین جوشکاری سفارشیساز را با عنوان SlimLine برای تولید قطعات اگزوز موتورهای جت به یک تولیدکننده در صنعت هوافضا عرضه کرد. قطعات از آلیاژهای دمای بالا ساخته شدهاند. یک ربات هر قطعه را برداشته و و داخل ورودی دستگاه جوش قرار میدهد، قطعه در عرض 1 ثانیه جوشکاری شده و سپس ربات قطعات جوشکاری شده را روی نوار نقاله قرار میدهد.
جوشکاری نقطهای در واقع در حال گذراندن نوعی رنسانس است. بعد از اینکه جوشکاری نقطهای در سال 1885 توسط مهندس الیو تومسون کشف شد، این روش تا اوایل قرن بیستم بهآهستگی رشد کرد و مورد استقبال قرار گرفت. سپس فناوریهایی همچون جوش لیزری (Laser Welding)، جوش همزن اصطکاکی (Friction Stir Welding) و جوشکاری با قوس الکتریکی (Advanced Arc Welding) فناوریهای آینده دنیای جوشکاری تلقی شدند. با این وجود، امروزه، ماشین کنترلهای پیشرفته با بهبود فرآیندهای عملیاتی خود باعث شدهاند تا ماشینهای جوشکاری نقطهای جایگاه خود را بهعنوان روش برتر جوشکاری باز پس بگیرند.
جوشکاری نقطهای رایجترین نوع جوشکاری مقاومتی محسوب میشود. یک سیستم جوشکاری مقاومتی نقطهای رایج و معمول از یک منبع تغذیه (که به کنترلر جوشکاری معروف است)، یک ترانسفورمر، یک یا چند هد جوشکاری، الکترودهای مثبت و منفی، و البته یک مانیتور تشکیل میشود. منبع تغذیه معمولا یا از فناوری حلقه باز و یا حلقه بسته استفاده میکند.
فناوری حلقه بسته شامل جریان مستقیم (DC) خطی و یک اینورتر فرکانس (High Frequency Inverter) بالاست. هر دو نوع به تغییر مقاومت در هر 10 تا 250 میکروثانیه پاسخ مناسبی نشان دادهاند. در نتیجه پارامتر برنامهریزی شده (جریان، ولتاژ یا توان) را برای داشتن جوشهای سازگارتر، ثابت نگه میدارد.
بهگفتۀ یکی از مهندسان شرکت T.J. Snow Co.، فناوریهای حلقه باز عمر طولانیتری دارند و شامل تخلیۀ خازن (capacitor discharge) و انرژی مستقیم (AC-جریان متناوب) هستند. این دسته از فناوریها معمولا فیدبکی ندارند و بیشتر در معرض سایش الکترود و چالشهای مربوط به قرارگیری قطعه هستند.
با توجه به گرانی انرژی در عصر حاضر، ترانسفورمرهای AC دیگر محبوب نیستند و بیشترین تقاضا مربوط به ترانسفورمرهای MFDC است که از نوع جریان مستقیم و فرکانس متوسط هستند. شرکت رومان (RoMan) بزرگترین تولیدکنندۀ ترانسفورمرهای استاندارد و سفارشی برای دستگاههای جوشهای مقاومتی است. تقریبا 85 درصد از تمامی دستگاههای جوش در آمریکا از ترانسفورمرهای این شرکت استفاده میکنند. طیف ترانسفورمرهای این شرکت از 12 کیلوگرم تا 5 تن بسته به دستگاه جوشکاری متنوع است. بر اساس تحقیقات این شرکت، بسیاری از ترانسفورمرهای قدیمی و AC این شرکت همچنان مورد استفاده هستند که این موضوع خوشایندی محسوب نمیشود. چرا که تیم تحقیقاتی RoMan ثابت کرد که با تغییر دستگاههای AC به نوع جدید و با کیفیت MFDC باعث کاهش 70 درصدی مصرف برق میشود.
هد جوش در جوشکاری نقطهای به شکلهای متنوعی از جمله دستی، پنوماتیک، سروو موتوری و الکترومغناطیسی وجود دارد. دینامیک هد جوش بستگی به پارامترهای مختلفی دارد که میتوان به نوع حرکت، نحوۀ تماس با قطعه، فاصله با قطعه، نیرو، میزان حرارت و مدت زمان جوش روی قطعه اشاره کرد.
الکترودهای جوشکاری نقطهای بهطور مستقیم، غیرمستقیم، موازی یا سری پیکربندی میشوند. مواد نوک آنها شامل آلیاژ مس، اکسید آلومینیوم، آلیاژ بریلیوم کبالت مس، مولیبدن، تنگستن و آلیاژ تنگستن مس است.
فرآیند جوشکاری نقطهای میتواند بهصورت نیمهاتوماتیک یا کاملا اتوماتیک (خودکار) عمل کند و یا در یک خط مونتاژ قرار گیرد. در راهاندازی یک ایستگاه نیمهاتوماتیک، اُپراتور قطعات را در قسمت فیکسچر قرار میدهد و از دکمههای دوتایی یا سوئیچ پایی برای جوشکاری استفاده میکند و پس از اتصال قطعات را از خط خارج میکند.
یک ایستگاه کاملا خوکار (تمام اتوماتیک) معمولا مجهز به ربات ششمحوره است که برداشتن، حرکت دادن و انتقال قطعات به قسمت جوشکاری و بعد از آن انتقال به نوار نقاله را برعهده دارد. در این نوع از سیستمها تمامی عملیات بهصورت خودکار و توسط ربات انجام میشوند.
جوشکاری نقطهای را میتوان از جمله مقاومترین انواع جوش دانست که متغیرهای زیادی ندارد و با کمترین میزان ورودی، اُپراتور قادر به انجام عملیات است.
از دیگر محصولات عایق کاری میتوان به نورد ورق نیز اشاره کرد
منبع: های تک ماشین